Utah Manufacturing Company Producing 10,000 PPE Face Shields Per Shift
- arichards42
- May 11, 2022
- 3 min read
In the first quarter of 2020, Jim Holbrook, of Premier Plastics, Inc. was anticipating another fast-paced year in manufacturing for he and his team, celebrating 30 years in business and looking to capitalize on increased manufacturing prospects in the US. “My personal goal was to increase new client sales by one-million dollars for 2020.” I knew it would be a lofty goal, but achievable through aggressive marketing strategies and promising new market verticals. A late-night news program on drive-thru testing facilities and the disturbing images of frontline health care providers ill equipped for the task at hand re-prioritized that goal for the time being, and it was on.” In Jim’s words!
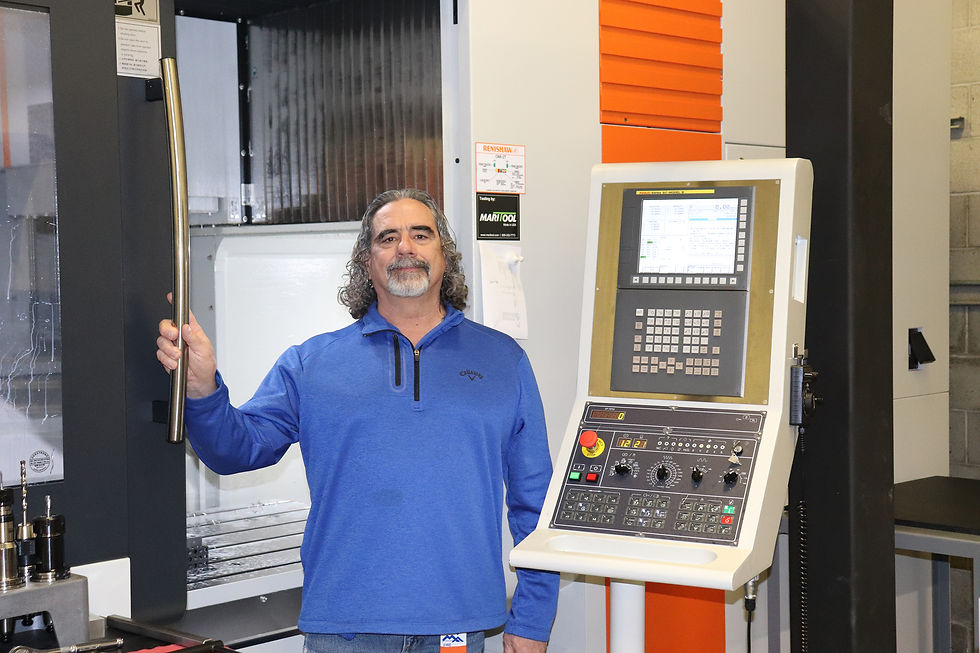
Reports had been circulating towards the end of 2019 about a strain of Corona virus and the possibilities of an on-coming pandemic. COVID-19 was rearing its nasty head in Wuhan China. Current records to date estimates there are *3.21 million cases of COVID-19 world-wide, resulting in 228,000 deaths. Here at home in the US we have experienced *1.06 million cases of COVID-19 resulting in 61,514 deaths. To put that number in perspective, that is more lives lost than lost in the Vietnam war.
That late-night news report highlighting the struggles of frontline workers, and the lack of PPE supplies captured the plight of the pandemic in one image; one health care provider with a face shield, one health care provider without a face shield. “That image played over and over in my head, surfacing often and with each new news clip. We are a manufacturing company, we are geared for this type of production, what can we do to help? Reports of 3D printed masks began to emerge, telling of limited production capabilities and high costs per unit, yet still a gallant attempt by companies and individuals alike to help slow the spread of COVID-19. 3D printed shields became the rage. “We have 3D printers but felt there had to be a more viable solution to the cause at hand. The health care industry needed these items in mass and needed them immediately” And so, it began…the quest to mass produce quality PET face shields for the health care providers on the front lines.

To those of us that know manufacturing in general, and thermoforming specifically, we know the process and time that goes into each and every project. Expediting the thermoforming process is not an easy task! However, by pulling resources and team members together, and dedicating 20% of their manufacturing capacity, Premier Plastics’ engineers, production team and a committed effort from several business partners, they took the challenge to heart, designing, prototyping, tooling, production, distribution and messaging in as little as two weeks. “We took a look at the mask designs that were out there and formulated a strategy to create a functional, high quality, cost effective, environmentally safe face shield. Hence, Project Shield! The brainchild of Jim Holbrook.

Nearly 9,300 U.S. health care workers contracted COVID-19, and 27 have died. A majority of those who tested positive (55%) think they were exposed while at work. **
To date, Premier Plastics, Inc. has manufactured and distributed over 100,000-100% Post-Consumer, 100% Recyclable PET face shields to hospitals across the nation, as well as local and regional health organizations, small companies and the hard hit, Navajo Reservation.
Goals are set to be achieved, and given time and energy, those goals can become a reality. However, as in all of life’s paths we walk, goals are only as strong as the contributions we choose to make along the way. Making personal and professional sacrifices in pursuit of the goals, makes achieving them…all the more rewarding.
* Source: Wikipedia
** Source: NPR
Comments